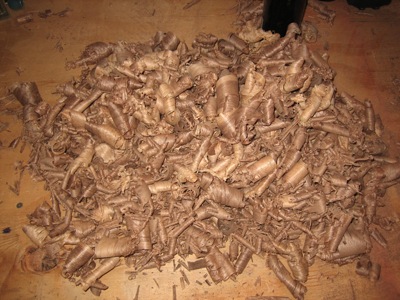
Continued from Part 1.
Coffins are traditionally bent at the shoulder. To this end the coffin maker uses a coffin maker's saw to cut several kerfs on the interior of the two boards that will become the sides. I tried that last time, but was unable to get a satisfactory bend or any bend for that matter. As far as I know there are three main ways of encouraging wood to bend. They are: lamination, ammonia, and steam. Of the three ammonia or steam made the most sense for the coffin, but ammonia smells bad and makes the wood a bit gray so steam seemed like the way to go. I didn't want to build a steam box so I took out the tin foil and fired up the stove.
I did several test bends in scrap to find a kerf width, angle and shape that would allow the shoulders to fit snugly against the sides of the rabbet. I timed each steam session to give me an idea of how long to leave the pieces on the fire (10 mins worked fine at this small size). When I had everything dialed I sawed the kerfs into the shoulders of the coffin sides. I used the side of a rasp to get the bottom nice and flat while the water came to a boil. The first side bent really nicely. It looks very modern, except for the ring I burned into it because of my stinginess with the tinfoil. The sap wood on the second piece didn't bend as nicely as the heart wood on the first. The outside of the bend had superficial cracking, but it still felt reasonably strong even though it lacks the fantastic plastic look of the first bend.
I took the bent sides and the head and foot and wiggled them all together. They fit snugly, and were pinned in place with nails from above and below. Then the sides were slid onto the bottom panel's rabbet and glued and clamped in place.
Once the glue had dried I shaved down the tails and pins and trued the bottom to the sides.
I wanted to pre-drill for the nails through the top but couldn't find my drill bits. Rather than call a friend to borrow one I made a D-bit out of a small metal pin I found on the street. D bits are different than a regular twist bit in three ways: they don't have spiral flutes, they don't cut as fast a a regular bit, and you can use a file, grinder, sidewalk or stone to make one out of almost any round piece of steel.
I drilled holes in the corners with the D-bit and tapped in a few nails to keep the lid registered while I drilled the rest of the nail holes.
After the top was planed flush to the sides I used a cabinet scraper to clean up tool marks, burns, bacon grease etc. The edges got a quick chamfer and I gave the whole thing a once over before grabbing a rag and applying Qualasole. I try to put on light enough coats so the finish can dry as Im applying it, and keep the pad moving all the time. After a good coating has built up I polish it with the pad nearly dry. I really like qualasole although I would say the effect is more polyurathane than french polish. One of my roommates says it looks like church furniture polish.
I'll take him at his word.
R.I.P Gandalf.
|
Gandalf's owner is a Brit, and in her state of grief must have reverted to writing the date DD/MM/YY. Two and a half weeks to get around to starting the coffin, half a week building it, a week for writing, photo editing, etc...Gandalf spent her last three weeks above ground chillin' in the freezer.
(very nice job brother)